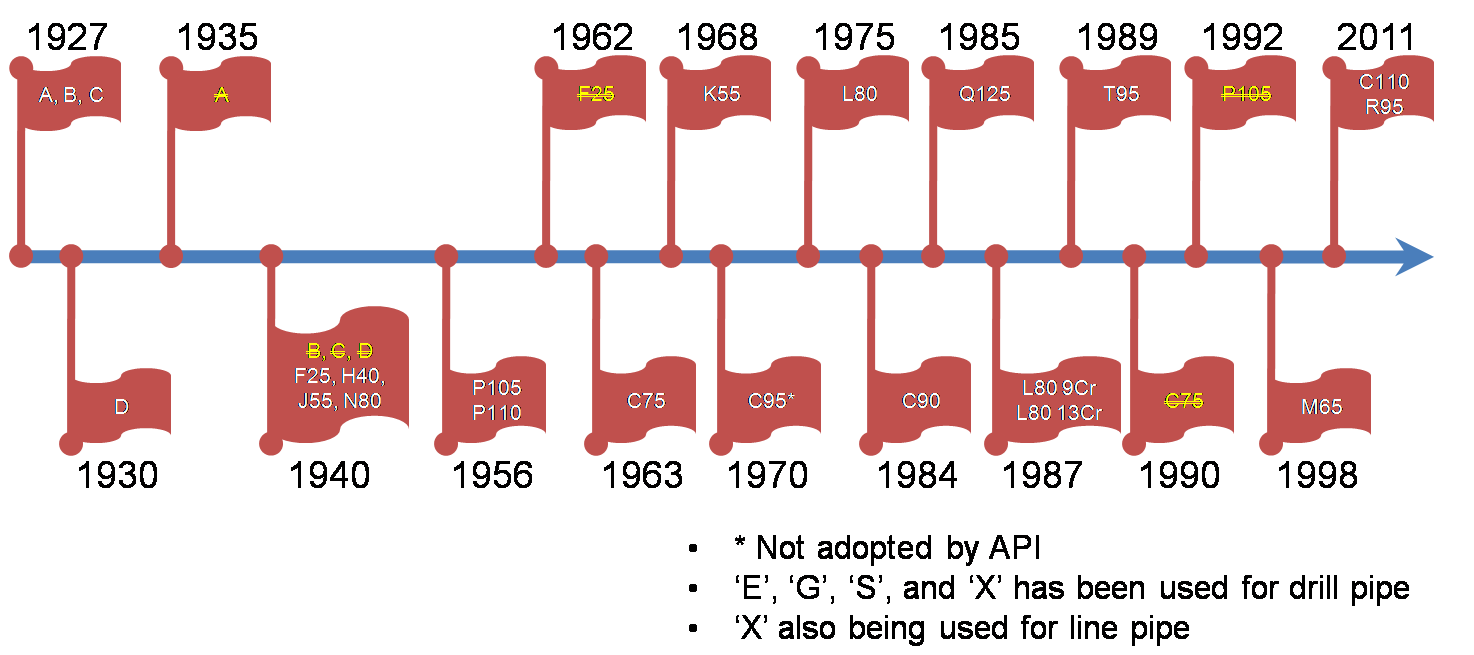
Most people who work in upstream oil industry aware about casing and tubing as has been established under API Specification 5CT. There are twelve (12) casing grade mentioned at the latest API 5CT standard (9th Edition) started with ‘H’, the weakest up to ‘Q’, the strongest from mechanical yield strength perspective.
Initially, pipe casing grade was identified solely by letter which used for phonetic clarity reason. This idea was stemming from agreement between pipe special committee in 1938. It was agreed since that time to identify pipe grade with a combination of letter and numeral. Numeral value indicates specified minimum yield strength while letter was used for phonetic clarity reason. It was decided not to use letters which had not been used previously or were not used by any manufacturer to designate their pipe product.
As the industry moving forward, hardcore demand creates new challenge. Several revisions also done on API specifications either removing or add new casing grade in order to align with industry application. However, this challenge was impact not only to manufacturer, but also to operator. One of the impacts was proposition to adopt new casing grade with used letter marking by some operator. The used letter was proposed with reason though it beats the phonetic clarity benefit of grading designation. Below are the summaries of API casing grade history.
Grade A, B, and C
The first three alphabetic letters were translated from low (30ksi yield), medium (35ksi yield), high carbon steel pipe (45ksi yield), respectively, which manufactured by seamless process in 1927. Another manufacturing process, Electric Resistant Welding (ERW) also permitted for this grade since the process was added to API Spec 5A in 1934.
Grade D
This grade was adopted in API Standard 5A since 1930 with 55ksi yield which became “the highest strength grade” that day to serve deeper well.
Grade F25, H40, J55, N80
Based on institute annual meeting decision in 1938, pipe grading system shall incorporate letter and number. It was agreed to use letters which hadn’t been used previously or weren’t use by any manufacturer to designate any pipe, which would be distinguishable readily when stamped on the pipe with a steel die and had no resemblance in sound to each other. The next grade was named F25, H40, J55, and N80. Most likely, ‘I’ letter wasn’t used due to obvious reason mentioned earlier.
J55 was adopted to replace the existing grade D even it has lower tensile strength properties (75k) with consideration it could be furnished with by seamless or ERW process.
In 1940, grade F25 was removed due to economic consideration since it costs similar with next higher grade (H40). Higher strength with higher performance would be preferable in price manner.
Grade P110 & P105
In 1956, new higher casing grade P110 was included in API Standard 5A. In 1960, P110 was taken from API Standard 5A and was incorporated into new API tentative standard 5AX along with P105 tubing.
Initially, higher strength 110k yield on both casing tubing was demanded by user. However, manufacturer had some difficulty to produce 110k yield for tubing that time. Hence, it was decided P grade on tubing come with 105k yield. Along with advance manufacturing technology and as requested by API user member, P110 also being done in tubing, and P105 grade was deleted in 1992 from API Spec 5CT.
Grade C75
In late 1950, more challenge was driven by one particular user member as they need to secure the casing for sour service well. It was known that casing/tubing need to have maximum 22HRC for sour service even up to this moment.
While the Q&T process were not available from manufacturing technology side at that time, another casing grade C75 as a modification of N80 tubular with normalized and tempering (N&T) ‘hardness controlled’ was produced. Those reason also become the philosophy behind API Tentative Standard 5AC creation. Along with this case, other user member also started to be warned for using P110 or P105 grade as those high strength casing are prone to sulphide embrittlement.
Grade K55
In 1968, it was reported that actual tensile seamless J55 grade always exceed 95k, more than minimum tensile strength of grade D drill pipe. Some proposition was offered to API for updating the J55 minimum tensile strength specification to 95k. API decided to come up with a new grade K55 considering 95k tensile properties on J55 were difficult to achieve by ERW process.
Grade C95
The grade was proposed by one user member as they mention it was better than existing grade C75 for mild sour service with 95k yield. However, this particular grade wasn’t adapted to API standard while many users also oppose this adoption since it’s not suitable for severe sour service.
Grade L80
As the advance of manufacturing process quench and temper (Q&T) technology and requested by many user members to raise the minimum 75k yield strength requirement for sour service, new grade L80 was born and became the current accepted grade for sour service replacing C75. Another variant of L80 with 9Cr and 13Cr was adopted in 1987.
Grade C90
In 1984, the user member insisted to use the letter ‘C’ for new 90ksi restricted yield strength to show better performance against C75 for similar sour service application. The benefit of name clarity was lost due to adoption of this grade (later on C75 was removed in 1990 which high likely to keep maintain name clarity benefit).
Grade Q125
This grade was adopted in 1985 to meet general service grade for deeper well.
Grade T95
In 1989, this grade was adopted by API for severe sour service requirement. The letter was selected to prevent name confusion with existing 95k yield grade (C95). It has more stringent quality control in a similar manner like C90 with 25.4HRC maximum hardness.
Grade M65
Another variant grade was adopted by API which not used so often. This is the only steel grade among general service with controlled maximum hardness.
Grade R95
This grade adopted by API with the same strength as T95 without hardness requirement which intended not for sour service.
Grade C110
As being driven by NACE MR0175-98 which addressed minimum 100k, 105k, and 110ksi yield strength tubular grade, this new casing grade finally being adopted by API in 2011 for sour service after numerous test. Special concern for proper controlled metallurgical attributes needs to be taken when using this particular grade.
Source:
- Dunlop, C.A.: “Trend and Developments in API Standards”, paper API-39-361 presented at spring meeting, Southwestern District, Division of Production, San Antonio, Texas, Mar 1939.
- Thomas, P.D.: “Steels for Oilwell Casing and Tubing – Past, Present, and Future”, paper SPE 527 presented at 92nd Annual AIME meeting, Dallas, Texas, USA, Feb 24-28, 1963.
- Speel, Lutz: “High Pressure Gas Well Completion”, paper WPC-12243 conference, 1967
- Bartlett, L.E., et al.: “Activities of the API Committee on Standardization of Tubular Goods”, paper SPE 20814 first presented at Offshore Technology Conference held in Houston, May 7-10, 1990.
- Jones, W.T.; N. Dharma: “Standardisation of Tubular Goods for Worldwide Application”, paper SPE 25328 presented at SPE Asia Pacific Oil and Gas Conference in Singapore, 8-10 February 1993.
- Economides, Michael J. et al., Petroleum Well Construction, John Wiley & Son, Ltd. 1997
- Urband, bruce E.: “High Strength Sour Service C110 Casing”, paper SPE/IADC 52843 presented at 1999 SPE/IADC Drilling Conference held in Amsterdam, Holland, 9-11 March 1999.
- Casner Engineering Service, “The History of API OCTG Grades”, November, 6, 2005.
- Urband, Bruce E.: “High Strength Sour Service C110 Casing”, paper SPE/IADC 52843 presented at 1999 SPE/IADC Drilling Conference held in Amsterdam, Holland, 9-11 March 1999.
- Chelette, K.D., et al.: “Management of Residual Stress: An Emerging Technology for Oil Industry Tubular Products”, paper OTC 22760 presented at Offshore Technology Conference Brazil held in Rio de Janeiro, Brazil, 4-6 October 2011.
- API Specification 5CT 9th Edition, 2011. Specification for Casing and Tubing.
- sovonex.com/drilling-equipment/api-casing/api-5ct-casing-grades/ (accessed at February, 13th, 2016).